Vous avez entendu parler de la méthode 5S, mais vous ne savez pas ce qu’elle implique exactement ? Elle est considérée comme un outil très important dans l’amélioration des performances et le développement des organisations.
Dans cet article, nous vous expliquons la définition et le fonctionnement de la méthode 5S, ainsi que ses avantages et bienfaits, notamment en termes d’amélioration de la productivité, d’optimisation de la sécurité et de diminution des déchets. Décryptage.
Qu’est-ce que la méthode 5S ?
Vous êtes à la recherche de précisions sur la méthode 5S ? Vous souhaitez en savoir plus sur ses principes et ses avantages ? Dans ce qui suit, nous allons vous expliquer en quoi consiste cette méthodologie et comment celle-ci s’applique. Nous vous donnerons également un aperçu des bénéfices qu’elle apporte.
Définition de la méthode 5S
La méthode 5S est une méthode d’organisation des lieux de travail qui a été développée au Japon. Elle a pour but d’améliorer la qualité, la productivité et le bien-être des employés.
Elle est basée sur les cinq principes suivants :
-
-
- Seiri (trier).
- Seiton (organiser).
- Seiso (nettoyer).
- Seiketsu (standardiser).
- Shitsuke (discipliner).
-
Ces principes sont appliqués de façon conjointe pour atteindre leurs objectifs.
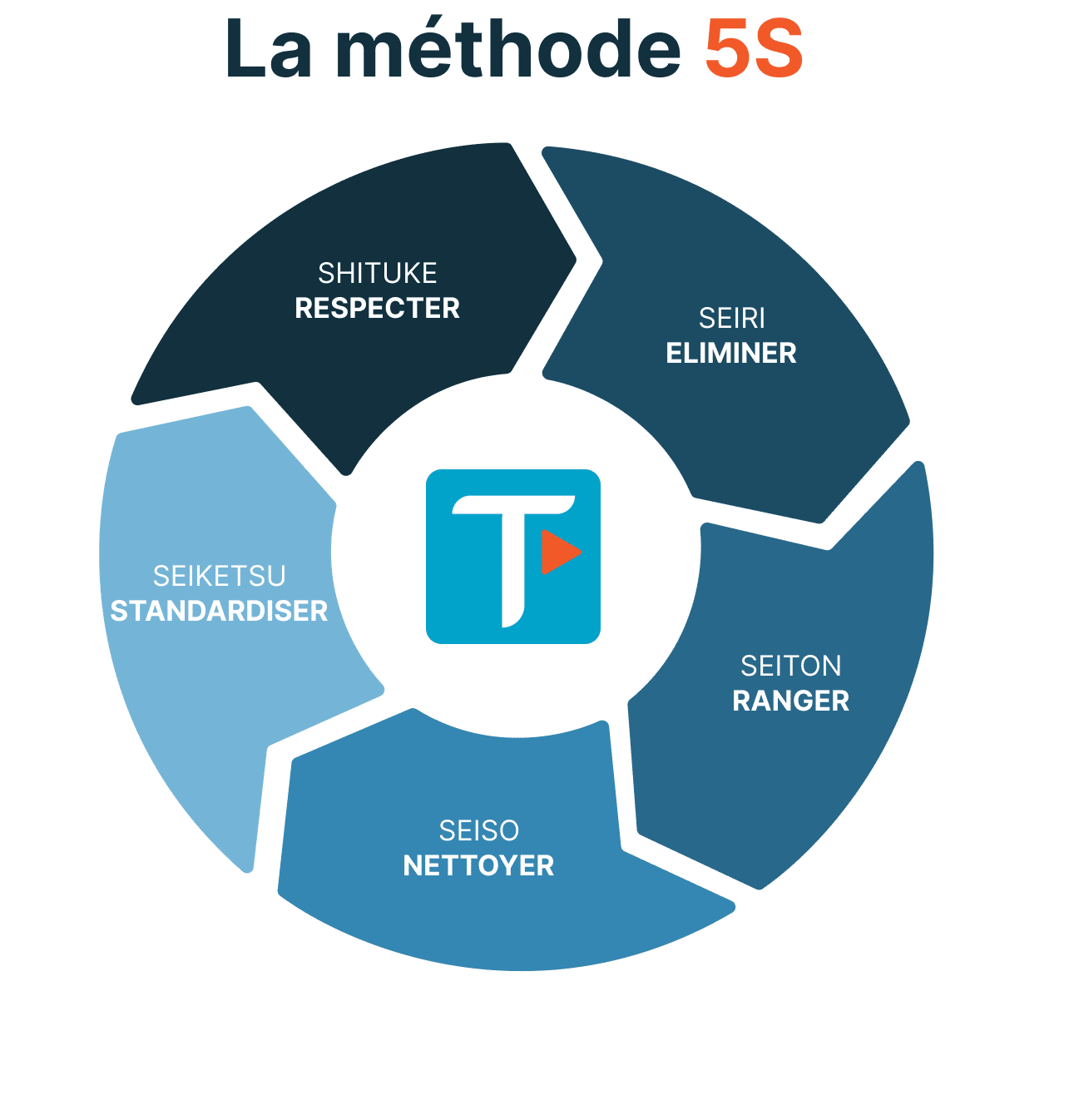
Les avantages et applications de la méthode 5S
Cette approche favorise la bonne utilisation des ressources et la prise de décision rapide et efficace. Elle s’utilise dans des secteurs comme l’industrie, le commerce ou les services.
Entre autres, elle permet de :
-
-
- Améliorer l’environnement de travail.
- Gain de temps dans la recherche des outils et matériels.
- Réduction des déchets et des coûts.
- Identification et résolution des problèmes.
- Augmentation des performances et de la qualité.
-
Ainsi, la méthode a des impacts positifs sur la productivité et la qualité des services et des produits. Elle est souvent utilisée en conjonction avec d’autres méthodes d’amélioration continue telles que le Lean Manufacturing ou le Kaizen.
Histoire et origine de la méthode 5S
Vous vous demandez peut-être comment la méthode 5S a vu le jour ? Pour répondre à cette question, la méthode 5S a été créée au Japon il y a plus de 60 ans.
C’était à l’époque où l’entreprise Toyota Motor Corporation a cherché à mettre en place un système de gestion des opérations. Le but était de fournir un espace de travail organisé et propice à la productivité des employés.
Par la suite, cette approche a été adoptée par de nombreuses entreprises à travers le monde, et son objectif est de réduire les pertes et d’améliorer la qualité des produits ainsi que la satisfaction des clients.
Comment fonctionne la méthode 5S ?
Cette méthode japonaise se divise en cinq étapes. Ce système est principalement utilisé dans le domaine industriel et a un objectif précis : améliorer l’efficacité et optimiser le travail.
Première étape de la méthode 5S : Seiri (trier)
La première étape de Seiri consiste à trier et à éliminer les objets ou outils inutiles.
Deuxième étape de la méthode 5S : Seiton (organiser).
Puis, vient Seiton, qui est l’organisation des outils et des informations restantes. Le but est de les disposer de façon optimale et logique pour faciliter l’accès aux équipes.
Troisième étape de la méthode 5S : Seiso (nettoyer).
Ensuite, Seiso est le nettoyage et l’entretien des outils et des documents. Il s’agit de les maintenir en bon état pour une meilleure durabilité et une utilisation optimale.
Quatrième étape de la méthode 5S : Seiketsu (standardiser).
Seiketsu, ce terme désigne la standardisation des processus. L’objectif est de mettre en place des procédures uniformisées pour favoriser le travail et l’échange d’informations entre les équipes.
Cinquième étape de la méthode 5S : Shitsuke (discipliner).
La dernière étape, Shitsuke, concerne la discipline. Il s’agit de maintenir les principes et les procédures mises en place pour garantir un bon fonctionnement des processus.
Avantages et bienfaits
Vous souhaitez en savoir plus sur les avantages de la méthode 5S ? Vous trouverez ci-dessous des informations complémentaires et des points de vue différents sur le sujet. Nous allons vous donner une perspective différente pour comprendre les avantages et bienfaits que peut apporter cette méthodologie.
Amélioration de la productivité
L’amélioration de la productivité est l’un des principaux avantages de la méthode 5S, et cela se manifeste à travers plusieurs bienfaits.
- Réduction du temps de recherche : en optimisant le rangement et le classement des objets et outils, et en rendant plus facile leur identification et leur utilisation.
- Renforcement de la qualité des produits finis : grâce à une meilleure utilisation des ressources et à une plus grande précision dans les processus de fabrication et de production.
- Augmentation de la concentration et de la productivité des employés : en leur offrant un environnement de travail plus organisé et plus propice à l’efficacité.
Optimisation de la sécurité
L’un des principaux avantages de la méthode 5S est son impact sur la sécurité. En optimisant l’utilisation des espaces de travail, l’entreprise peut réduire le nombre d’accidents et améliorer la prévention des risques.
Les employés peuvent ainsi travailler dans un environnement sûr. Cela génère plus de confiance et de respect chez les employés, ce qui peut à son tour contribuer à améliorer les performances et la productivité globales.
De plus, grâce à la méthode 5S, les entreprises peuvent réduire leurs coûts de santé et de sécurité, ce qui peut également être un avantage pour leurs finances.
Diminution des déchets
L’utilisation de ce genre de méthode permet de réduire considérablement les déchets et d’améliorer l’efficacité des processus.
En effet, le principe de la méthode 5S est de supprimer tout ce qui est superflu et de ne garder que ce qui est nécessaire pour le processus.
Elle permet également de réduire la consommation d’énergie tout en veillant à la qualité du produit fini.
La mise en œuvre de la méthode 5S est très simple et peut s’adapter à toute situation. Elle offre de nombreux bénéfices à court et long terme sur la réduction de la consommation d’énergie et la qualité du produit.. N’hésitez pas à appliquer ses principes pour améliorer vos processus et votre productivité.
FAQ
Quelle est la définition de la méthode 5S ?
La méthode 5S est une méthodologie d’amélioration continue qui a pour objectif d’optimiser le fonctionnement des entreprises et des organisations. Elle se compose de cinq principes : Seiri (tri), Seiton (rangement), Seiso (nettoyage), Seiketsu (standardisation) et Shitsuke (discipline).
Quel est son fonctionnement ?
Les cinq principes de la méthode 5S sont appliqués successivement pour améliorer l’efficacité et la productivité des processus de l’entreprise. La première étape consiste à trier les objets, documents et outils inutiles afin de gagner en espace et en temps. La seconde étape consiste à organiser les objets, documents et outils existants pour optimiser leur accessibilité. La troisième étape consiste à nettoyer les surfaces et équipements afin d’améliorer l’hygiène et la santé au travail. La quatrième étape consiste à standardiser les processus pour assurer un fonctionnement optimal et durable. Enfin, la cinquième étape consiste à instaurer une discipline dans le respect des règles établies.
Quels en sont les avantages ?
La méthode 5S permet aux entreprises et aux organisations d’améliorer significativement leur efficacité et leur productivité grâce à une meilleure organisation des différents outils, documents et objets nécessaires au bon fonctionnement de l’entreprise. Elle permet également une meilleure hygiène et santé au travail ainsi qu’une optimisation des processus pour un fonctionnement optimal et durable.
Quelle en est l’origine ?
La méthode 5S a été développée au Japon dans les années 1950 par Toyota Motor Corporation afin d’améliorer l’efficacité et la productivité de ses usines. Depuis, elle a été adoptée par plusieurs entreprises à travers le monde.
Comment la mettre en place ?
Pour mettre en place la méthode 5S, il est nécessaire de former le personnel à cette méthodologie afin que chacun comprenne bien son fonctionnement et ses bénéfices potentiels. Une fois que tous les employés connaissent bien les principes de la mise en œuvre, ils doivent s’engager à respecter rigoureusement les procédures définies par chaque étape du processus.